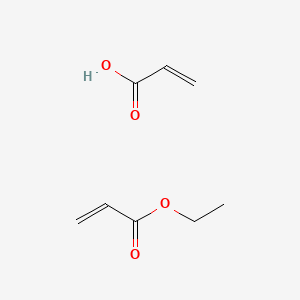
2-Propenoic acid, polymer with ethyl 2-propenoate
Overview
Description
2-Propenoic acid, polymer with ethyl 2-propenoate is a useful research compound. Its molecular formula is C8H12O4 and its molecular weight is 172.18 g/mol. The purity is usually 95%.
BenchChem offers high-quality 2-Propenoic acid, polymer with ethyl 2-propenoate suitable for many research applications. Different packaging options are available to accommodate customers' requirements. Please inquire for more information about 2-Propenoic acid, polymer with ethyl 2-propenoate including the price, delivery time, and more detailed information at info@benchchem.com.
properties
CAS RN |
25085-35-2 |
---|---|
Product Name |
2-Propenoic acid, polymer with ethyl 2-propenoate |
Molecular Formula |
C8H12O4 |
Molecular Weight |
172.18 g/mol |
IUPAC Name |
ethyl prop-2-enoate;prop-2-enoic acid |
InChI |
InChI=1S/C5H8O2.C3H4O2/c1-3-5(6)7-4-2;1-2-3(4)5/h3H,1,4H2,2H3;2H,1H2,(H,4,5) |
InChI Key |
XHIOOWRNEXFQFM-UHFFFAOYSA-N |
SMILES |
CCOC(=O)C=C.C=CC(=O)O |
Canonical SMILES |
CCOC(=O)C=C.C=CC(=O)O |
Origin of Product |
United States |
Synthesis routes and methods I
Procedure details
Synthesis routes and methods II
Procedure details
Disclaimer and Information on In-Vitro Research Products
Please be aware that all articles and product information presented on BenchChem are intended solely for informational purposes. The products available for purchase on BenchChem are specifically designed for in-vitro studies, which are conducted outside of living organisms. In-vitro studies, derived from the Latin term "in glass," involve experiments performed in controlled laboratory settings using cells or tissues. It is important to note that these products are not categorized as medicines or drugs, and they have not received approval from the FDA for the prevention, treatment, or cure of any medical condition, ailment, or disease. We must emphasize that any form of bodily introduction of these products into humans or animals is strictly prohibited by law. It is essential to adhere to these guidelines to ensure compliance with legal and ethical standards in research and experimentation.