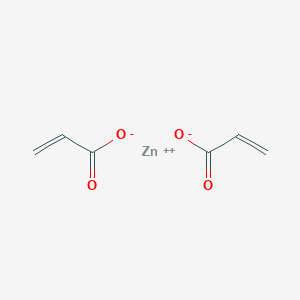
Zinc acrylate
Overview
Description
Synthesis Analysis
The synthesis of zinc acrylate involves chemoselective transesterification processes, where hard zinc alkoxide generation facilitates the selective transformation of acrylate derivatives. This method, utilizing catalytic zinc clusters and dimethylamino)pyridine, allows for the production of functionalized acrylate derivatives under mild conditions, showcasing the chemical versatility and efficiency of zinc acrylate synthesis (Nakatake, Yazaki, & Ohshima, 2016).
Molecular Structure Analysis
The molecular structure of zinc acrylate compounds, such as dichloro(ethylenediamine-N,N-di-3-propionato)zinc, has been elucidated through various spectroscopic and crystallographic techniques. These studies reveal the coordination polyhedra around zinc atoms and provide insights into the geometric and electronic structures that underpin the reactivity and properties of zinc acrylate derivatives (Tsirul’nikova et al., 2017).
Chemical Reactions and Properties
Zinc acrylate undergoes various chemical reactions, demonstrating its reactivity and functional versatility. The compound is involved in polymerization processes, where it acts as a catalyst or reactant to form polyacrylate materials with high molecular weight and specific properties. Such reactivity is fundamental to its application in creating functional polymers and materials (Garner et al., 2006).
Physical Properties Analysis
The physical properties of zinc acrylate, including its solubility, thermal stability, and polymerization characteristics, have been extensively studied. These properties are crucial for its application in the synthesis of copolymers and composites, where its ability to improve material performance and durability is leveraged (Xie Zhi-pen, 2014).
Chemical Properties Analysis
The chemical behavior of zinc acrylate, particularly in reactions leading to the formation of composites and nanomaterials, underscores its utility in materials science. The synthesis of zinc oxide nanoparticle-loaded polymers demonstrates the potential of zinc acrylate in creating advanced materials with desirable optical, electronic, and mechanical properties (Bajpai, Jadaun, & Tiwari, 2016).
Scientific Research Applications
Summary of the Application
Zinc-based acrylate copolymers (ZnPs) are used in marine antifouling applications. They are designed to prevent marine biofouling, a severe problem affecting ocean exploitation and utilization .
Methods of Application or Experimental Procedures
ZnPs are synthesized using a bifunctional zinc acrylate monomer (ZnM) as a new self-polishing monomer, and three acrylate monomers (namely, methyl methacrylate, ethyl acrylate, and 2-methoxyethyl acrylate) are used as comonomers . The antifouling coatings are prepared using these ZnPs as the matrix material .
Results or Outcomes
The prepared coatings showed excellent antifouling performance, inhibiting the settlement of barnacles in both the South China Sea for 9 months and in the Yellow Sea for at least 15 months . They also exhibited ideal antifouling properties with little silt and biological mucosa adhered to the surface after 6 months, and corresponding coatings exhibited little biofouling after 16 months in the ocean .
2. Production of Specialty Rubber Products
Summary of the Application
Zinc Acrylate is primarily used in the production of specialty rubber products such as belts and hoses for automobiles .
Results or Outcomes
The outcomes of this application are the production of specialty rubber products such as belts and hoses for automobiles .
3. Self-Polishing Coatings
Summary of the Application
Zinc acrylate is used in the synthesis of self-polishing copolymers for marine anti-biofouling applications .
Methods of Application or Experimental Procedures
Self-polishing copolymers containing two different Zinc acrylate monomers in varying ratios are designed and synthesized .
Results or Outcomes
The outcomes of this application are the production of self-polishing coatings that are effective for marine anti-biofouling in static or low flow conditions .
4. Geo-Construction
Summary of the Application
Zinc acrylate is used to stabilize steep slopes in construction, highway cuts, and other disturbed soils in geo-construction .
Results or Outcomes
The outcomes of this application are the stabilization of steep slopes in construction, highway cuts, and other disturbed soils .
5. Self-Polishing Coatings
Summary of the Application
Zinc acrylate is used in the synthesis of self-polishing copolymers for marine anti-biofouling applications .
Methods of Application or Experimental Procedures
Self-polishing copolymers containing two different Zinc acrylate monomers in varying ratios are designed and synthesized .
Results or Outcomes
The outcomes of this application are the production of self-polishing coatings that are effective for marine anti-biofouling in static or low flow conditions .
6. Geo-Construction
Summary of the Application
Zinc acrylate is used to stabilize steep slopes in construction, highway cuts, and other disturbed soils in geo-construction .
Results or Outcomes
The outcomes of this application are the stabilization of steep slopes in construction, highway cuts, and other disturbed soils .
Safety And Hazards
Future Directions
The results of a study highlight that the biocidal ZnP-based coatings are highly promising candidates for marine antifouling applications . The grafted BIT–zinc acrylate resin not only exhibits excellent antifouling properties but also a significant self-polishing performance, providing a novel strategy to design a long-term antifouling resin with stable antifoulant release .
properties
IUPAC Name |
zinc;prop-2-enoate | |
---|---|---|
Source | PubChem | |
URL | https://pubchem.ncbi.nlm.nih.gov | |
Description | Data deposited in or computed by PubChem | |
InChI |
InChI=1S/2C3H4O2.Zn/c2*1-2-3(4)5;/h2*2H,1H2,(H,4,5);/q;;+2/p-2 | |
Source | PubChem | |
URL | https://pubchem.ncbi.nlm.nih.gov | |
Description | Data deposited in or computed by PubChem | |
InChI Key |
XKMZOFXGLBYJLS-UHFFFAOYSA-L | |
Source | PubChem | |
URL | https://pubchem.ncbi.nlm.nih.gov | |
Description | Data deposited in or computed by PubChem | |
Canonical SMILES |
C=CC(=O)[O-].C=CC(=O)[O-].[Zn+2] | |
Source | PubChem | |
URL | https://pubchem.ncbi.nlm.nih.gov | |
Description | Data deposited in or computed by PubChem | |
Molecular Formula |
C6H6O4Zn | |
Source | PubChem | |
URL | https://pubchem.ncbi.nlm.nih.gov | |
Description | Data deposited in or computed by PubChem | |
Related CAS |
79-10-7 (Parent) | |
Record name | Zinc acrylate | |
Source | ChemIDplus | |
URL | https://pubchem.ncbi.nlm.nih.gov/substance/?source=chemidplus&sourceid=0014643879 | |
Description | ChemIDplus is a free, web search system that provides access to the structure and nomenclature authority files used for the identification of chemical substances cited in National Library of Medicine (NLM) databases, including the TOXNET system. | |
DSSTOX Substance ID |
DTXSID1027768 | |
Record name | Zinc acrylate | |
Source | EPA DSSTox | |
URL | https://comptox.epa.gov/dashboard/DTXSID1027768 | |
Description | DSSTox provides a high quality public chemistry resource for supporting improved predictive toxicology. | |
Molecular Weight |
207.5 g/mol | |
Source | PubChem | |
URL | https://pubchem.ncbi.nlm.nih.gov | |
Description | Data deposited in or computed by PubChem | |
Physical Description |
Dry Powder | |
Record name | 2-Propenoic acid, zinc salt (2:1) | |
Source | EPA Chemicals under the TSCA | |
URL | https://www.epa.gov/chemicals-under-tsca | |
Description | EPA Chemicals under the Toxic Substances Control Act (TSCA) collection contains information on chemicals and their regulations under TSCA, including non-confidential content from the TSCA Chemical Substance Inventory and Chemical Data Reporting. | |
Product Name |
Zinc acrylate | |
CAS RN |
14643-87-9 | |
Record name | Zinc acrylate | |
Source | ChemIDplus | |
URL | https://pubchem.ncbi.nlm.nih.gov/substance/?source=chemidplus&sourceid=0014643879 | |
Description | ChemIDplus is a free, web search system that provides access to the structure and nomenclature authority files used for the identification of chemical substances cited in National Library of Medicine (NLM) databases, including the TOXNET system. | |
Record name | 2-Propenoic acid, zinc salt (2:1) | |
Source | EPA Chemicals under the TSCA | |
URL | https://www.epa.gov/chemicals-under-tsca | |
Description | EPA Chemicals under the Toxic Substances Control Act (TSCA) collection contains information on chemicals and their regulations under TSCA, including non-confidential content from the TSCA Chemical Substance Inventory and Chemical Data Reporting. | |
Record name | Zinc acrylate | |
Source | EPA DSSTox | |
URL | https://comptox.epa.gov/dashboard/DTXSID1027768 | |
Description | DSSTox provides a high quality public chemistry resource for supporting improved predictive toxicology. | |
Record name | Zinc acrylate | |
Source | European Chemicals Agency (ECHA) | |
URL | https://echa.europa.eu/substance-information/-/substanceinfo/100.035.160 | |
Description | The European Chemicals Agency (ECHA) is an agency of the European Union which is the driving force among regulatory authorities in implementing the EU's groundbreaking chemicals legislation for the benefit of human health and the environment as well as for innovation and competitiveness. | |
Explanation | Use of the information, documents and data from the ECHA website is subject to the terms and conditions of this Legal Notice, and subject to other binding limitations provided for under applicable law, the information, documents and data made available on the ECHA website may be reproduced, distributed and/or used, totally or in part, for non-commercial purposes provided that ECHA is acknowledged as the source: "Source: European Chemicals Agency, http://echa.europa.eu/". Such acknowledgement must be included in each copy of the material. ECHA permits and encourages organisations and individuals to create links to the ECHA website under the following cumulative conditions: Links can only be made to webpages that provide a link to the Legal Notice page. | |
Record name | ZINC ACRYLATE | |
Source | FDA Global Substance Registration System (GSRS) | |
URL | https://gsrs.ncats.nih.gov/ginas/app/beta/substances/4720M0PK19 | |
Description | The FDA Global Substance Registration System (GSRS) enables the efficient and accurate exchange of information on what substances are in regulated products. Instead of relying on names, which vary across regulatory domains, countries, and regions, the GSRS knowledge base makes it possible for substances to be defined by standardized, scientific descriptions. | |
Explanation | Unless otherwise noted, the contents of the FDA website (www.fda.gov), both text and graphics, are not copyrighted. They are in the public domain and may be republished, reprinted and otherwise used freely by anyone without the need to obtain permission from FDA. Credit to the U.S. Food and Drug Administration as the source is appreciated but not required. | |
Synthesis routes and methods I
Procedure details
Synthesis routes and methods II
Procedure details
Synthesis routes and methods III
Procedure details
Synthesis routes and methods IV
Procedure details
Synthesis routes and methods V
Procedure details
Retrosynthesis Analysis
AI-Powered Synthesis Planning: Our tool employs the Template_relevance Pistachio, Template_relevance Bkms_metabolic, Template_relevance Pistachio_ringbreaker, Template_relevance Reaxys, Template_relevance Reaxys_biocatalysis model, leveraging a vast database of chemical reactions to predict feasible synthetic routes.
One-Step Synthesis Focus: Specifically designed for one-step synthesis, it provides concise and direct routes for your target compounds, streamlining the synthesis process.
Accurate Predictions: Utilizing the extensive PISTACHIO, BKMS_METABOLIC, PISTACHIO_RINGBREAKER, REAXYS, REAXYS_BIOCATALYSIS database, our tool offers high-accuracy predictions, reflecting the latest in chemical research and data.
Strategy Settings
Precursor scoring | Relevance Heuristic |
---|---|
Min. plausibility | 0.01 |
Model | Template_relevance |
Template Set | Pistachio/Bkms_metabolic/Pistachio_ringbreaker/Reaxys/Reaxys_biocatalysis |
Top-N result to add to graph | 6 |
Feasible Synthetic Routes
Citations
Disclaimer and Information on In-Vitro Research Products
Please be aware that all articles and product information presented on BenchChem are intended solely for informational purposes. The products available for purchase on BenchChem are specifically designed for in-vitro studies, which are conducted outside of living organisms. In-vitro studies, derived from the Latin term "in glass," involve experiments performed in controlled laboratory settings using cells or tissues. It is important to note that these products are not categorized as medicines or drugs, and they have not received approval from the FDA for the prevention, treatment, or cure of any medical condition, ailment, or disease. We must emphasize that any form of bodily introduction of these products into humans or animals is strictly prohibited by law. It is essential to adhere to these guidelines to ensure compliance with legal and ethical standards in research and experimentation.