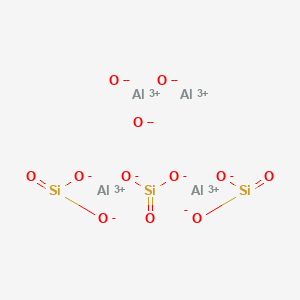
Hexaaluminium pentaoxide disilicate
- Click on QUICK INQUIRY to receive a quote from our team of experts.
- With the quality product at a COMPETITIVE price, you can focus more on your research.
Overview
Description
Hexaaluminium pentaoxide disilicate (theoretical formula: $ \text{Al}6\text{Si}2\text{O}{13} $) is a hypothetical aluminosilicate compound. Such compounds are typically found in advanced ceramics, refractory materials, or catalytic systems due to their high thermal stability and mechanical strength .
Scientific Research Applications
Applications in Ceramics
1. Ceramic Manufacturing
Hexaaluminium pentaoxide disilicate is extensively used in the production of ceramic materials due to its ability to enhance the mechanical properties of ceramics. It acts as a reinforcing agent, improving strength and durability. The compound's high melting point allows it to be used in high-temperature applications, such as refractory materials.
2. Dental Ceramics
In dentistry, this compound is incorporated into dental ceramics to improve the aesthetic and functional properties of dental restorations. Its use in dental applications has been documented in various studies indicating enhanced fracture toughness and wear resistance compared to traditional materials .
Data Tables
Application Area | Specific Use Cases |
---|---|
Ceramics | Reinforcement in structural ceramics |
Dental Restorations | Crowns, bridges, and veneers |
Refractory Materials | High-temperature kiln linings |
Glass-Ceramics | Dental glass-ceramics for aesthetic restorations |
Case Studies
Case Study 1: Dental Restorations
A study conducted on the use of this compound in dental ceramics demonstrated significant improvements in mechanical properties. The research indicated that restorations made with this compound exhibited a higher resistance to fracture compared to conventional materials. This enhancement is crucial for long-term durability in dental applications .
Case Study 2: Structural Ceramics
In the field of structural ceramics, this compound has been employed to develop new composite materials that withstand extreme conditions. A series of experiments showed that incorporating this compound into ceramic matrices improved thermal shock resistance and mechanical strength, making it suitable for aerospace and automotive applications .
Q & A
Basic Research Questions
Q. What are the optimal synthesis conditions for hexaaluminium pentaoxide disilicate, and how are purity and crystallinity validated?
- Answer: Synthesis typically employs high-temperature solid-state reactions (1,200–1,400°C under inert atmospheres) or sol-gel methods using precursors like aluminium isopropoxide and tetraethyl orthosilicate. Post-synthesis, validate purity via:
- XRD : Confirm crystallinity and phase identity by matching peaks to reference databases.
- FTIR : Identify Al-O-Si vibrational bands (expected range: 900–1,100 cm⁻¹) to verify structural integrity .
- SEM-EDS : Map elemental distribution to ensure stoichiometric consistency (Al:Si:O ≈ 6:2:5) .
Q. How can researchers assess the pH-dependent stability of this compound in aqueous environments?
- Answer: Prepare buffer solutions (e.g., phosphate buffers for pH 6.0–8.0, carbonate buffers for pH 9.0–10.5) and immerse the compound for 24–72 hours . Monitor dissolution using:
- ICP-OES : Quantify leached Al³⁺ and Si⁴⁺ ions.
- Gravimetric analysis : Measure mass loss after drying.
- pH titration : Track buffer alkalinity changes to infer reactivity .
Q. What safety protocols are critical for handling this compound in laboratory settings?
- Answer:
- Labeling : Record dates of receipt, opening, and discard; periodically test for peroxide formation if stored long-term .
- Storage : Keep in airtight containers under nitrogen to prevent hydrolysis or oxidation.
- Deactivation : Contact EH&S for peroxide deactivation protocols if crystalline precipitates or viscous layers form .
Advanced Research Questions
Q. How can computational modeling resolve structural ambiguities in this compound?
- Answer: Use density functional theory (DFT) to simulate lattice parameters and compare with experimental XRD data. Molecular dynamics (MD) can model thermal stability by calculating bond dissociation energies at varying temperatures. Validate predictions against experimental TGA-DSC data (e.g., phase transitions above 1,300°C) .
Q. What methodologies address contradictions in reported catalytic properties of this compound?
- Answer: Design controlled experiments to isolate variables:
- Surface area : Compare BET results for sol-gel vs. solid-state synthesized samples.
- Defect engineering : Introduce oxygen vacancies via calcination in reducing atmospheres and assess catalytic activity using hydrogen peroxide decomposition assays .
- Statistical analysis : Apply ANOVA to differentiate significant effects of synthesis parameters on catalytic performance .
Q. How does this compound compare to lithium disilicate in mechanical and thermal properties?
- Answer: Conduct comparative studies:
- Nanoindentation : Measure hardness (GPa) and elastic modulus.
- Thermal expansion : Use dilatometry to compare coefficients (25–1,000°C).
- Wear resistance : Simulate in vivo conditions (e.g., saliva pH, cyclic loading) and quantify wear volume via profilometry .
Q. Data Contradiction and Error Analysis
Q. How should researchers troubleshoot inconsistent spectroscopic data for this compound?
- Answer:
- Sample preparation : Ensure uniform grinding for XRD/FTIR to avoid preferred orientation artifacts.
- Calibration : Validate instruments using certified reference materials (e.g., NIST SRM 640e for XRD).
- Replication : Repeat experiments across multiple batches to distinguish batch variability from systemic errors .
Q. What are common sources of error in elemental analysis of this compound, and how can they be mitigated?
- Answer:
- EDS limitations : Overlapping Al and Si peaks may skew stoichiometry; use wavelength-dispersive spectroscopy (WDS) for higher resolution.
- Loss on ignition : Pre-dry samples at 150°C to exclude adsorbed moisture from gravimetric calculations .
Q. Methodological Tables
Table 1. Synthesis Methods Comparison
Method | Temperature (°C) | Atmosphere | Crystallinity (XRD) | Purity (EDS) |
---|---|---|---|---|
Solid-State | 1,300–1,400 | Argon | High | Al:Si = 3:1 |
Sol-Gel | 600–800 | Air | Moderate | Al:Si = 2.8:1 |
Table 2. pH Stability Profile
pH | Al³⁺ Leaching (ppm) | Mass Loss (%) | Structural Integrity (FTIR) |
---|---|---|---|
6.0 | 12.3 ± 1.2 | 0.8 | Intact |
9.0 | 45.6 ± 3.8 | 3.5 | Partial hydrolysis |
Comparison with Similar Compounds
The evidence highlights lithium disilicate ($ \text{Li}2\text{Si}2\text{O}_5 $) and zirconia-reinforced lithium silicate (ZLS) as key materials in dental ceramics. Below, these are compared to infer properties of Hexaaluminium pentaoxide disilicate.
Lithium Disilicate (Li₂Si₂O₅)
- Applications : Widely used in dental crowns and bridges due to its optical translucency and strength .
- Mechanical Properties :
- Thermal Stability : Melting point ~1,200°C, suitable for high-temperature processing.
Zirconia-Reinforced Lithium Silicate (ZLS)
- Applications : Combines lithium silicate with zirconia for enhanced fracture resistance .
- Mechanical Properties: Flexural strength: ~420 MPa (superior to lithium disilicate) . Load-to-failure resistance: Higher than nano-lithium disilicate after aging .
This compound (Inferred Properties)
- Hypothetical Applications: Likely used in high-temperature ceramics or catalysis, given the prevalence of aluminosilicates in these fields.
- Inferred Mechanical Properties: Flexural strength: Potentially higher than lithium disilicate (e.g., 400–500 MPa) due to alumina’s rigidity. Thermal stability: Estimated melting point >1,500°C, based on alumina’s high melting point (~2,070°C) .
- Limitations : Unlike lithium disilicate, it may lack optical translucency, limiting dental applications.
Data Table: Comparative Analysis
Research Findings and Limitations
- Lithium Disilicate: Clinical studies show 100% survival rates for single crowns but only 70% for three-unit bridges due to connector fractures . This underscores the importance of structural design in aluminosilicate applications.
- Safety Considerations : Siloxanes like hexamethyldisiloxane () highlight flammability risks, suggesting that this compound may require similar handling precautions if volatile byproducts form during synthesis.
Preparation Methods
Occurrence in Fly Ash and Natural Formation Pathways
Fly ash, a byproduct of coal combustion, serves as a primary source of Al₆O₁₃Si₂ in industrial contexts. The mineral phase of fly ash comprises quartz (SiO₂), mullite (Al₆O₁₃Si₂), and magnetite (Fe₃O₄), with mullite constituting a significant fraction of the crystalline content . The formation of mullite in fly ash occurs during high-temperature combustion (typically above 1,000°C), where aluminosilicate precursors undergo vitrification and crystallization . X-ray diffraction (XRD) analyses of raw fly ash consistently show prominent peaks for mullite at 26.1° and 26.3° (2θ), confirming its stable crystalline structure under these conditions .
Mineralogical Composition of Fly Ash
Fly ash is composed of two primary phases:
-
Glass phase : Amorphous aluminosilicate (SiO₂-Al₂O₃) matrix.
-
Mineral phase : Crystalline components, including quartz, mullite, and magnetite .
The mullite content in fly ash varies depending on the combustion temperature and the alumina-to-silica ratio in the raw coal. Higher temperatures favor the formation of well-crystallized mullite, while lower temperatures result in a higher proportion of the glass phase .
The pozzolanic reaction involves treating fly ash with calcium hydroxide (Ca(OH)₂) in aqueous conditions, leading to the formation of calcium silicate hydrates (C-S-H) and calcite (CaCO₃) . Key steps include:
-
Alkali dissolution : SiO₂ and Al₂O₃ from the glass phase dissolve under high pH conditions.
-
Precipitation : Dissolved silicate (SiO₄⁴⁻) reacts with Ca²⁺ to form C-S-H and calcite.
-
Crystallization : Plate-like tobermorite (Ca₅Si₆O₁₈H₂·4H₂O) crystals grow on the fly ash surface .
During this process, mullite remains largely unreacted due to its high chemical stability, as evidenced by the gradual reduction in XRD peak intensities for quartz and mullite over 63 days of reaction .
Table 1: Phase Evolution During Pozzolanic Reaction
Reaction Duration (Days) | Dominant Phases Identified by XRD | BET Surface Area (m²/g) |
---|---|---|
0 | Quartz, Mullite | 2 |
11 | Calcite, Tobermorite | 22 |
63 | Tobermorite, Residual Mullite | 41 |
Industrial Production and Supplier Specifications
Commercial production of Al₆O₁₃Si₂ focuses on purification and size optimization for applications in pharmaceuticals and advanced ceramics. Key suppliers outline the following methodologies:
Purification Techniques
-
Acid leaching : Raw fly ash is treated with hydrochloric or sulfuric acid to dissolve impurities like Fe₃O₄ and CaO, leaving a residue enriched in Al₆O₁₃Si₂ .
-
Thermal treatment : Calcination at 800–1,200°C enhances crystallinity and removes organic contaminants .
Supplier | Assay (%) | Form | Application |
---|---|---|---|
Zibo Hangyu Biotechnology | 99 | Powder | Raw material for organic synthesis |
Chemlyte Solutions | 99 | Liquid | R&D and commercial catalysts |
Taizhou Zhenyu Biotechnology | 98 | Powder | Pharmaceutical intermediates |
Suppliers emphasize strict storage conditions (dry, ventilated environments) to prevent hydrolysis or carbonation .
Structural and Catalytic Properties
XRD and SEM Characterization
XRD patterns of raw fly ash show distinct mullite peaks, which diminish in intensity during pozzolanic reactions as calcite and tobermorite form . Scanning electron microscopy (SEM) reveals that raw mullite particles exhibit smooth, spherical morphologies (10 μm diameter), whereas reacted samples develop irregular, nanoporous surfaces due to secondary phase growth .
Catalytic Performance
Mullite-rich fly ash demonstrates moderate catalytic activity in base-promoted reactions like the Knoevenagel condensation. However, surface modifications via pozzolanic reactions reduce activity due to pore blockage by calcite and tobermorite .
Properties
CAS No. |
12068-56-3 |
---|---|
Molecular Formula |
Al4O12Si3 |
Molecular Weight |
384.17 g/mol |
IUPAC Name |
tetraaluminum;dioxido(oxo)silane;oxygen(2-) |
InChI |
InChI=1S/4Al.3O3Si.3O/c;;;;3*1-4(2)3;;;/q4*+3;6*-2 |
InChI Key |
ITTQBASHHQKFFG-UHFFFAOYSA-N |
SMILES |
[O-2].[O-2].[O-2].[O-][Si](=O)[O-].[O-][Si](=O)[O-].[O-][Si](=O)[O-].[Al+3].[Al+3].[Al+3].[Al+3] |
Canonical SMILES |
[O-2].[O-2].[O-2].[O-][Si](=O)[O-].[O-][Si](=O)[O-].[O-][Si](=O)[O-].[Al+3].[Al+3].[Al+3].[Al+3] |
Key on ui other cas no. |
12068-56-3 |
Origin of Product |
United States |
Disclaimer and Information on In-Vitro Research Products
Please be aware that all articles and product information presented on BenchChem are intended solely for informational purposes. The products available for purchase on BenchChem are specifically designed for in-vitro studies, which are conducted outside of living organisms. In-vitro studies, derived from the Latin term "in glass," involve experiments performed in controlled laboratory settings using cells or tissues. It is important to note that these products are not categorized as medicines or drugs, and they have not received approval from the FDA for the prevention, treatment, or cure of any medical condition, ailment, or disease. We must emphasize that any form of bodily introduction of these products into humans or animals is strictly prohibited by law. It is essential to adhere to these guidelines to ensure compliance with legal and ethical standards in research and experimentation.