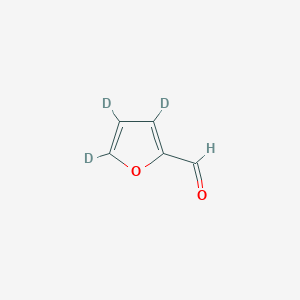
Furfural-3,4,5-D3
概要
説明
Furfural-3,4,5-D3 is a variant of furfural, a commodity chemical derived from biomass . It is used in synthetic chemistry and is available as a high-quality, certified reference material .
Synthesis Analysis
Furfural, the parent compound of Furfural-3,4,5-D3, is produced from biomass, specifically from the hydrolysis of pentosan polymers in biomass to pentose sugars (xylose) which undergo acid catalysis under high temperatures . The exact synthesis process for Furfural-3,4,5-D3 is not explicitly mentioned in the search results.Molecular Structure Analysis
The molecular formula of Furfural-3,4,5-D3 is C5HD3O2 . The exact structure is not provided in the search results.Chemical Reactions Analysis
Furfural, from which Furfural-3,4,5-D3 is derived, can be converted into a variety of chemicals and fuels. This includes the production of furfurylamine, C6 carboxylic acid (i.e., furandicarboxylic acid), furfural alcohol, aromatics, levulinic acid, maleic acid, succinic acid, furoic acid, and cyclopentanone .Physical And Chemical Properties Analysis
Furfural-3,4,5-D3 is an oil with a light yellow to dark yellow color . It is hygroscopic and should be stored in a refrigerator under an inert atmosphere . More specific physical and chemical properties are not provided in the search results.科学的研究の応用
Biomass-Derived Chemical Production
Furfural, derived from lignocellulosic biomass, is a key renewable platform compound for sustainable chemical production. Its highly functionalized molecular structure makes it suitable for creating value-added chemicals containing oxygen atoms. Various catalytic processes have been explored to convert furfural into C4 and C5 chemicals, with hydrogenation and hydrogenolysis being significant steps in this conversion (Li, Jia, & Wang, 2016).
Biorefining and Heterogeneous Catalysis
In the context of green chemistry, heterogeneously catalyzed processes for furfural production are preferred due to their environmental benefits. These processes facilitate easier separation and recovery of the catalyst, produce less waste, and are less corrosive. The challenge lies in identifying active and stable water-tolerant solid acid catalysts for this purpose (Karinen, Vilonen, & Niemelä, 2011).
Electrochemical Conversion for Biofuel Production
The electrochemical conversion of furfural to methylfuran (MF) and of 5-hydroxymethylfurfural (5-HMF) to 2,5-dimethylfuran (DMF) offers a path for storing electric energy in liquid organic fuels. This conversion is crucial for biofuel generation and represents an innovative approach in the field of renewable energy (Nilges & Schröder, 2013).
Catalytic Conversion to Diols
Furfural's catalytic conversion to 1,4-pentanediol (PD) in a single reactor represents a significant advancement. This process, which involves a combination of hydrogenation reactions and acid-catalyzed rearrangements, offers a promising route for synthesizing bio-based linear diols (Liu et al., 2018).
Enhancing Rheological Properties of Asphalt
Furfural has been used to improve the rheological properties of asphalt binders when combined with crumb rubber. This application in construction materials demonstrates furfural's versatility beyond the chemical industry (Shatanawi, Bíró, Geiger, & Amirkhanian, 2012).
Applications in the Leather Industry
Furfural's active aldehyde group has found long-term use in leather manufacturing. Its derivatives, such as 5-HMF, have been explored for use as tanning agents, showcasing furfural's applicability in diverse industrial sectors (Zhang, 2009).
Safety And Hazards
将来の方向性
Furfural, the parent compound of Furfural-3,4,5-D3, has been identified as a promising chemical platform directly derived from biomass . Its conversion into a variety of chemicals and fuels is an active area of research, with a focus on developing new catalytic processes that transform biomass into valuable products under competitive conditions . The future of Furfural-3,4,5-D3 likely lies in similar directions, although specific future directions for this compound are not provided in the search results.
特性
IUPAC Name |
3,4,5-trideuteriofuran-2-carbaldehyde | |
---|---|---|
Source | PubChem | |
URL | https://pubchem.ncbi.nlm.nih.gov | |
Description | Data deposited in or computed by PubChem | |
InChI |
InChI=1S/C5H4O2/c6-4-5-2-1-3-7-5/h1-4H/i1D,2D,3D | |
Source | PubChem | |
URL | https://pubchem.ncbi.nlm.nih.gov | |
Description | Data deposited in or computed by PubChem | |
InChI Key |
HYBBIBNJHNGZAN-CBYSEHNBSA-N | |
Source | PubChem | |
URL | https://pubchem.ncbi.nlm.nih.gov | |
Description | Data deposited in or computed by PubChem | |
Canonical SMILES |
C1=COC(=C1)C=O | |
Source | PubChem | |
URL | https://pubchem.ncbi.nlm.nih.gov | |
Description | Data deposited in or computed by PubChem | |
Isomeric SMILES |
[2H]C1=C(OC(=C1[2H])C=O)[2H] | |
Source | PubChem | |
URL | https://pubchem.ncbi.nlm.nih.gov | |
Description | Data deposited in or computed by PubChem | |
Molecular Formula |
C5H4O2 | |
Source | PubChem | |
URL | https://pubchem.ncbi.nlm.nih.gov | |
Description | Data deposited in or computed by PubChem | |
Molecular Weight |
99.10 g/mol | |
Source | PubChem | |
URL | https://pubchem.ncbi.nlm.nih.gov | |
Description | Data deposited in or computed by PubChem | |
Product Name |
Furfural-3,4,5-D3 |
Synthesis routes and methods I
Procedure details
Synthesis routes and methods II
Procedure details
Synthesis routes and methods III
Procedure details
Synthesis routes and methods IV
Procedure details
Synthesis routes and methods V
Procedure details
Retrosynthesis Analysis
AI-Powered Synthesis Planning: Our tool employs the Template_relevance Pistachio, Template_relevance Bkms_metabolic, Template_relevance Pistachio_ringbreaker, Template_relevance Reaxys, Template_relevance Reaxys_biocatalysis model, leveraging a vast database of chemical reactions to predict feasible synthetic routes.
One-Step Synthesis Focus: Specifically designed for one-step synthesis, it provides concise and direct routes for your target compounds, streamlining the synthesis process.
Accurate Predictions: Utilizing the extensive PISTACHIO, BKMS_METABOLIC, PISTACHIO_RINGBREAKER, REAXYS, REAXYS_BIOCATALYSIS database, our tool offers high-accuracy predictions, reflecting the latest in chemical research and data.
Strategy Settings
Precursor scoring | Relevance Heuristic |
---|---|
Min. plausibility | 0.01 |
Model | Template_relevance |
Template Set | Pistachio/Bkms_metabolic/Pistachio_ringbreaker/Reaxys/Reaxys_biocatalysis |
Top-N result to add to graph | 6 |
Feasible Synthetic Routes
Citations
試験管内研究製品の免責事項と情報
BenchChemで提示されるすべての記事および製品情報は、情報提供を目的としています。BenchChemで購入可能な製品は、生体外研究のために特別に設計されています。生体外研究は、ラテン語の "in glass" に由来し、生物体の外で行われる実験を指します。これらの製品は医薬品または薬として分類されておらず、FDAから任何の医療状態、病気、または疾患の予防、治療、または治癒のために承認されていません。これらの製品を人間または動物に体内に導入する形態は、法律により厳格に禁止されています。これらのガイドラインに従うことは、研究と実験において法的および倫理的な基準の遵守を確実にするために重要です。