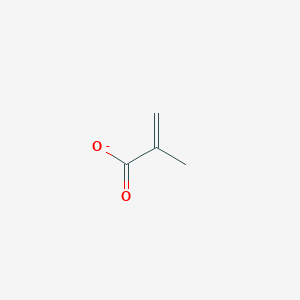
Methacrylate
Overview
Description
Methacrylate is a chemical compound that is widely used in scientific research due to its unique properties. Methacrylate is a monomer that can be polymerized to form a wide range of materials, including polymethyl methacrylate (PMMA), polyethylene glycol dimethacrylate (PEGDMA), and polyurethane methacrylate (PUMA). These materials have a wide range of applications in the fields of medicine, dentistry, and engineering.
Scientific Research Applications
Neurophysiological Research : Methacrylate, particularly polymethyl methacrylate, is used in neurophysiology for creating permanent apertures in the skull of monkeys for electrophysiological recording. A study described an alternative to polymethyl methacrylate by using a titanium chamber fastened with screws and sealed with hydroxyapatite to form a watertight gasket. This method promises increased durability and easier maintenance, benefiting both scientific discovery and animal welfare (Adams et al., 2011).
Microfluidics and Nanofluidics : Poly(methyl methacrylate) (PMMA) is used in the rapid prototyping of microfluidic devices. A study introduced a cost-effective bonding technique for PMMA layers, crucial for microfluidic research and its transition from laboratory to market. This technique allows for fast assembly of multilayer PMMA microfluidic devices, which is important for both academic research and industrial applications (Liga et al., 2016).
Dental Materials : Methacrylate-based materials, such as light-curing base materials, are significant in dentistry, especially for patients with acrylate intolerance. Research highlights the importance of choosing suitable base materials in the manufacture of dental prostheses to prevent clinical pathological manifestations due to intolerance (Sarkisyan et al., 2021).
Biomedical Applications : Methacrylate hydrogels, such as hydroxypropylmethacrylamid (HPMA) and 2-hydroxyethylmethacrylate (HEMA), have been used as scaffolds in spinal cord injury research. These hydrogels can be modified to improve tissue repair after spinal cord injury, showing potential for biomedical applications (Hejčl et al., 2018).
Tissue Engineering : Methacrylated hyaluronic acid (MeHA) is used in tissue engineering and drug delivery. A study proposed infrared spectroscopy as an alternative modality for assessing the degree of methacrylation of HA hydrogels, which is crucial for cell interactions in tissue engineering applications (Yousefi et al., 2018).
Environmental and Ecological Research : Methacrylates are studied for their environmental fate and aquatic toxicity. They are not considered persistent or bioaccumulative but have low to moderate toxicity. Research has developed quantitative structure–activity relationships (QSARs) to support the environmental assessment of methacrylic acid esters (Staples et al., 2009).
properties
CAS RN |
18358-13-9 |
---|---|
Product Name |
Methacrylate |
Molecular Formula |
C4H5O2- |
Molecular Weight |
85.08 g/mol |
IUPAC Name |
2-methylprop-2-enoate |
InChI |
InChI=1S/C4H6O2/c1-3(2)4(5)6/h1H2,2H3,(H,5,6)/p-1 |
InChI Key |
CERQOIWHTDAKMF-UHFFFAOYSA-M |
SMILES |
CC(=C)C(=O)[O-] |
Canonical SMILES |
CC(=C)C(=O)[O-] |
synonyms |
Methacrylic acidanion |
Origin of Product |
United States |
Synthesis routes and methods I
Procedure details
Synthesis routes and methods II
Procedure details
Synthesis routes and methods III
Procedure details
Synthesis routes and methods IV
Procedure details
Retrosynthesis Analysis
AI-Powered Synthesis Planning: Our tool employs the Template_relevance Pistachio, Template_relevance Bkms_metabolic, Template_relevance Pistachio_ringbreaker, Template_relevance Reaxys, Template_relevance Reaxys_biocatalysis model, leveraging a vast database of chemical reactions to predict feasible synthetic routes.
One-Step Synthesis Focus: Specifically designed for one-step synthesis, it provides concise and direct routes for your target compounds, streamlining the synthesis process.
Accurate Predictions: Utilizing the extensive PISTACHIO, BKMS_METABOLIC, PISTACHIO_RINGBREAKER, REAXYS, REAXYS_BIOCATALYSIS database, our tool offers high-accuracy predictions, reflecting the latest in chemical research and data.
Strategy Settings
Precursor scoring | Relevance Heuristic |
---|---|
Min. plausibility | 0.01 |
Model | Template_relevance |
Template Set | Pistachio/Bkms_metabolic/Pistachio_ringbreaker/Reaxys/Reaxys_biocatalysis |
Top-N result to add to graph | 6 |
Feasible Synthetic Routes
Disclaimer and Information on In-Vitro Research Products
Please be aware that all articles and product information presented on BenchChem are intended solely for informational purposes. The products available for purchase on BenchChem are specifically designed for in-vitro studies, which are conducted outside of living organisms. In-vitro studies, derived from the Latin term "in glass," involve experiments performed in controlled laboratory settings using cells or tissues. It is important to note that these products are not categorized as medicines or drugs, and they have not received approval from the FDA for the prevention, treatment, or cure of any medical condition, ailment, or disease. We must emphasize that any form of bodily introduction of these products into humans or animals is strictly prohibited by law. It is essential to adhere to these guidelines to ensure compliance with legal and ethical standards in research and experimentation.