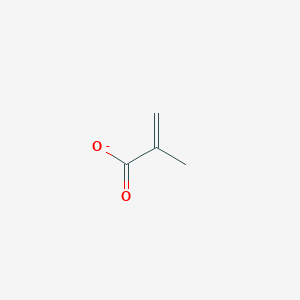
甲基丙烯酸酯
描述
Methacrylate is a chemical compound that is widely used in scientific research due to its unique properties. Methacrylate is a monomer that can be polymerized to form a wide range of materials, including polymethyl methacrylate (PMMA), polyethylene glycol dimethacrylate (PEGDMA), and polyurethane methacrylate (PUMA). These materials have a wide range of applications in the fields of medicine, dentistry, and engineering.
科学研究应用
神经生理学研究:甲基丙烯酸甲酯,特别是聚甲基丙烯酸甲酯,用于神经生理学中为猴子颅骨创建永久开口以进行电生理记录。一项研究描述了一种替代聚甲基丙烯酸甲酯的方法,即使用钛制腔室,用螺钉固定并用羟基磷灰石密封以形成密封垫。这种方法承诺提高耐用性和更易维护,有利于科学发现和动物福利 (Adams et al., 2011)。
微流体学和纳流体学:聚甲基丙烯酸甲酯(PMMA)用于微流体器件的快速原型制作。一项研究介绍了一种成本效益的PMMA层粘接技术,对于微流体研究及其从实验室向市场转化至关重要。这种技术允许快速组装多层PMMA微流体器件,对学术研究和工业应用都很重要 (Liga et al., 2016)。
牙科材料:基于甲基丙烯酸甲酯的材料,如光固化基材,在牙科中具有重要意义,特别适用于对丙烯酸不耐受的患者。研究强调了在制造牙修复体时选择合适的基材的重要性,以防止由于不耐受而导致临床病理表现 (Sarkisyan et al., 2021)。
生物医学应用:甲基丙烯酸酯水凝胶,如羟丙基甲基丙烯酰胺(HPMA)和2-羟基乙基甲基丙烯酸酯(HEMA),已用作脊髓损伤研究中的支架。这些水凝胶可以被改性以改善脊髓损伤后的组织修复,显示出生物医学应用的潜力 (Hejčl等,2018)。
组织工程:甲基化透明质酸(MeHA)用于组织工程和药物传递。一项研究提出了红外光谱作为评估HA水凝胶甲基化程度的替代方法,这对于组织工程应用中的细胞相互作用至关重要 (Yousefi et al., 2018)。
环境和生态研究:甲基丙烯酸酯被研究其在环境中的命运和水生毒性。它们不被认为是持久性或生物富集性的,但具有低至中等毒性。研究已经发展了定量结构-活性关系(QSARs)以支持甲基丙烯酸酯的环境评估 (Staples等,2009)。
属性
CAS 编号 |
18358-13-9 |
---|---|
产品名称 |
Methacrylate |
分子式 |
C4H5O2- |
分子量 |
85.08 g/mol |
IUPAC 名称 |
2-methylprop-2-enoate |
InChI |
InChI=1S/C4H6O2/c1-3(2)4(5)6/h1H2,2H3,(H,5,6)/p-1 |
InChI 键 |
CERQOIWHTDAKMF-UHFFFAOYSA-M |
SMILES |
CC(=C)C(=O)[O-] |
规范 SMILES |
CC(=C)C(=O)[O-] |
同义词 |
Methacrylic acidanion |
产品来源 |
United States |
Synthesis routes and methods I
Procedure details
Synthesis routes and methods II
Procedure details
Synthesis routes and methods III
Procedure details
Synthesis routes and methods IV
Procedure details
Retrosynthesis Analysis
AI-Powered Synthesis Planning: Our tool employs the Template_relevance Pistachio, Template_relevance Bkms_metabolic, Template_relevance Pistachio_ringbreaker, Template_relevance Reaxys, Template_relevance Reaxys_biocatalysis model, leveraging a vast database of chemical reactions to predict feasible synthetic routes.
One-Step Synthesis Focus: Specifically designed for one-step synthesis, it provides concise and direct routes for your target compounds, streamlining the synthesis process.
Accurate Predictions: Utilizing the extensive PISTACHIO, BKMS_METABOLIC, PISTACHIO_RINGBREAKER, REAXYS, REAXYS_BIOCATALYSIS database, our tool offers high-accuracy predictions, reflecting the latest in chemical research and data.
Strategy Settings
Precursor scoring | Relevance Heuristic |
---|---|
Min. plausibility | 0.01 |
Model | Template_relevance |
Template Set | Pistachio/Bkms_metabolic/Pistachio_ringbreaker/Reaxys/Reaxys_biocatalysis |
Top-N result to add to graph | 6 |
Feasible Synthetic Routes
体外研究产品的免责声明和信息
请注意,BenchChem 上展示的所有文章和产品信息仅供信息参考。 BenchChem 上可购买的产品专为体外研究设计,这些研究在生物体外进行。体外研究,源自拉丁语 "in glass",涉及在受控实验室环境中使用细胞或组织进行的实验。重要的是要注意,这些产品没有被归类为药物或药品,他们没有得到 FDA 的批准,用于预防、治疗或治愈任何医疗状况、疾病或疾病。我们必须强调,将这些产品以任何形式引入人类或动物的身体都是法律严格禁止的。遵守这些指南对确保研究和实验的法律和道德标准的符合性至关重要。