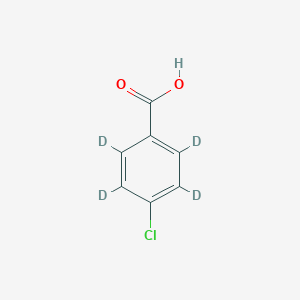
4-Chlorobenzoic Acid-d4
Overview
Description
4-Chlorobenzoic Acid, a derivative of benzoic acid, is a compound of interest due to its chemical and physical properties. It has a molecular formula of C7H5ClO2.
Synthesis Analysis
4-Chlorobenzoic acid can be synthesized through various chemical reactions. Notably, its derivatives and related compounds have been synthesized through different catalytic and condensation processes. For example, 4,5,6,7-Tetrachlorobenzo[d][1,3,2]dioxaborol-2-ol acts as an effective catalyst for the amide condensation of carboxylic acids and amines (Maki, Ishihara, & Yamamoto, 2006).
Molecular Structure Analysis
The molecular structure of 4-Chlorobenzoic Acid has been extensively studied. For instance, the crystal structure analysis reveals that the molecule is almost planar, with specific dihedral angles between its constituent groups (Gotoh, Katagiri, & Ishida, 2010).
Chemical Reactions and Properties
4-Chlorobenzoic Acid participates in various chemical reactions and has unique properties. It is used as a substrate in different catalytic reactions, as observed in studies on enzymes like 4-Chlorobenzoate:CoA ligase/synthetase (Gulick, Lu, & Dunaway-Mariano, 2004).
Scientific Research Applications
Environmental Monitoring and Degradation
Biodegradation Studies
Research conducted by Samadi et al. (2020) demonstrated the potential of Lysinibacillus macrolides DSM54T for the biodegradation of 4-Chlorobenzoic Acid (4-CBA), emphasizing the environmental relevance of this compound in the context of pollution and soil remediation. The study optimized conditions for the biodegradation process, showing significant removal efficiency of 4-CBA, highlighting its importance in bioremediation efforts for polluted soils (Samadi et al., 2020).
Degradation in Water Treatment
Lesage et al. (2014) investigated the degradation of 4-CBA using plasma dielectric barrier discharge (DBD) in water, exploring the efficiency of different electrode materials and the impact of discharge power and frequency on the treatment process. This study provides insights into advanced oxidation processes for the removal of 4-CBA from water, contributing to the development of more effective water treatment technologies (Lesage et al., 2014).
Chemical Interactions and Molecular Studies
Molecular Interactions
Research on the solvate of 4-Chlorobenzoic acid with N, N-dimethylformamide provided insights into the hydrogen bonding interactions and molecular arrangement, contributing to a deeper understanding of its chemical behavior and potential applications in the design of new molecular assemblies or materials (Xu et al., 2004).
Structural Analysis and Docking Studies
Sayed and Foro (2020) conducted an X-ray structural analysis of p-Chlorobenzoic acid, combined with DFT studies and in silico molecular docking on Tankyrase I enzyme. This work offers valuable information on the compound's potential inhibitory effects on specific enzymes, suggesting applications in drug discovery and the development of new therapeutic agents (Sayed & Foro, 2020).
properties
IUPAC Name |
4-chloro-2,3,5,6-tetradeuteriobenzoic acid | |
---|---|---|
Source | PubChem | |
URL | https://pubchem.ncbi.nlm.nih.gov | |
Description | Data deposited in or computed by PubChem | |
InChI |
InChI=1S/C7H5ClO2/c8-6-3-1-5(2-4-6)7(9)10/h1-4H,(H,9,10)/i1D,2D,3D,4D | |
Source | PubChem | |
URL | https://pubchem.ncbi.nlm.nih.gov | |
Description | Data deposited in or computed by PubChem | |
InChI Key |
XRHGYUZYPHTUJZ-RHQRLBAQSA-N | |
Source | PubChem | |
URL | https://pubchem.ncbi.nlm.nih.gov | |
Description | Data deposited in or computed by PubChem | |
Canonical SMILES |
C1=CC(=CC=C1C(=O)O)Cl | |
Source | PubChem | |
URL | https://pubchem.ncbi.nlm.nih.gov | |
Description | Data deposited in or computed by PubChem | |
Isomeric SMILES |
[2H]C1=C(C(=C(C(=C1C(=O)O)[2H])[2H])Cl)[2H] | |
Source | PubChem | |
URL | https://pubchem.ncbi.nlm.nih.gov | |
Description | Data deposited in or computed by PubChem | |
Molecular Formula |
C7H5ClO2 | |
Source | PubChem | |
URL | https://pubchem.ncbi.nlm.nih.gov | |
Description | Data deposited in or computed by PubChem | |
DSSTOX Substance ID |
DTXSID301006147 | |
Record name | 4-Chloro(~2~H_4_)benzoic acid | |
Source | EPA DSSTox | |
URL | https://comptox.epa.gov/dashboard/DTXSID301006147 | |
Description | DSSTox provides a high quality public chemistry resource for supporting improved predictive toxicology. | |
Molecular Weight |
160.59 g/mol | |
Source | PubChem | |
URL | https://pubchem.ncbi.nlm.nih.gov | |
Description | Data deposited in or computed by PubChem | |
Product Name |
4-Chlorobenzoic Acid-d4 | |
CAS RN |
85577-25-9 | |
Record name | 4-Chloro(~2~H_4_)benzoic acid | |
Source | EPA DSSTox | |
URL | https://comptox.epa.gov/dashboard/DTXSID301006147 | |
Description | DSSTox provides a high quality public chemistry resource for supporting improved predictive toxicology. | |
Synthesis routes and methods I
Procedure details
Synthesis routes and methods II
Procedure details
Synthesis routes and methods III
Procedure details
Synthesis routes and methods IV
Procedure details
Synthesis routes and methods V
Procedure details
Disclaimer and Information on In-Vitro Research Products
Please be aware that all articles and product information presented on BenchChem are intended solely for informational purposes. The products available for purchase on BenchChem are specifically designed for in-vitro studies, which are conducted outside of living organisms. In-vitro studies, derived from the Latin term "in glass," involve experiments performed in controlled laboratory settings using cells or tissues. It is important to note that these products are not categorized as medicines or drugs, and they have not received approval from the FDA for the prevention, treatment, or cure of any medical condition, ailment, or disease. We must emphasize that any form of bodily introduction of these products into humans or animals is strictly prohibited by law. It is essential to adhere to these guidelines to ensure compliance with legal and ethical standards in research and experimentation.