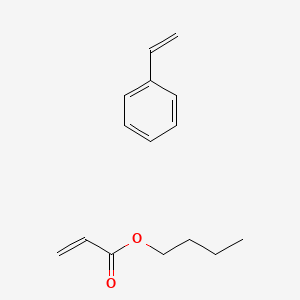
2-Propenoic acid, butyl ester, polymer with ethenylbenzene
Vue d'ensemble
Description
2-Propenoic acid, butyl ester, polymer with ethenylbenzene is a useful research compound. Its molecular formula is C15H20O2 and its molecular weight is 232.32 g/mol. The purity is usually 95%.
The exact mass of the compound 2-Propenoic acid, butyl ester, polymer with ethenylbenzene is unknown and the complexity rating of the compound is unknown. The storage condition is unknown. Please store according to label instructions upon receipt of goods.Use and application categories indicated by third-party sources: Cosmetics -> Film forming. However, this does not mean our product can be used or applied in the same or a similar way.
BenchChem offers high-quality 2-Propenoic acid, butyl ester, polymer with ethenylbenzene suitable for many research applications. Different packaging options are available to accommodate customers' requirements. Please inquire for more information about 2-Propenoic acid, butyl ester, polymer with ethenylbenzene including the price, delivery time, and more detailed information at info@benchchem.com.
Propriétés
Numéro CAS |
25767-47-9 |
---|---|
Nom du produit |
2-Propenoic acid, butyl ester, polymer with ethenylbenzene |
Formule moléculaire |
C15H20O2 |
Poids moléculaire |
232.32 g/mol |
Nom IUPAC |
butyl prop-2-enoate;styrene |
InChI |
InChI=1S/C8H8.C7H12O2/c1-2-8-6-4-3-5-7-8;1-3-5-6-9-7(8)4-2/h2-7H,1H2;4H,2-3,5-6H2,1H3 |
Clé InChI |
TUZBYYLVVXPEMA-UHFFFAOYSA-N |
SMILES |
CCCCOC(=O)C=C.C=CC1=CC=CC=C1 |
SMILES canonique |
CCCCOC(=O)C=C.C=CC1=CC=CC=C1 |
Autres numéros CAS |
25767-47-9 |
Origine du produit |
United States |
Synthesis routes and methods I
Procedure details
Synthesis routes and methods II
Procedure details
Synthesis routes and methods III
Procedure details
Synthesis routes and methods IV
Procedure details
Synthesis routes and methods V
Procedure details
Avertissement et informations sur les produits de recherche in vitro
Veuillez noter que tous les articles et informations sur les produits présentés sur BenchChem sont destinés uniquement à des fins informatives. Les produits disponibles à l'achat sur BenchChem sont spécifiquement conçus pour des études in vitro, qui sont réalisées en dehors des organismes vivants. Les études in vitro, dérivées du terme latin "in verre", impliquent des expériences réalisées dans des environnements de laboratoire contrôlés à l'aide de cellules ou de tissus. Il est important de noter que ces produits ne sont pas classés comme médicaments et n'ont pas reçu l'approbation de la FDA pour la prévention, le traitement ou la guérison de toute condition médicale, affection ou maladie. Nous devons souligner que toute forme d'introduction corporelle de ces produits chez les humains ou les animaux est strictement interdite par la loi. Il est essentiel de respecter ces directives pour assurer la conformité aux normes légales et éthiques en matière de recherche et d'expérimentation.